Clad Sheet Aluminum Alloy
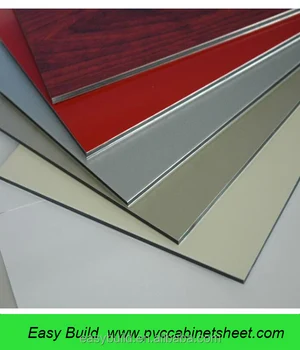
From this trade name the adjective clad and the verb cladding have been derived.
Clad sheet aluminum alloy. Alclad is a corrosion resistant aluminium sheet formed from high purity aluminium surface layers metallurgically bonded rolled onto to high strength aluminium alloy core material. Cladding is the bonding together of dissimilar metals it is different from fusion welding or gluing as a method to fasten the metals together. The fuselages of civil aircraft are for the most part made from 2024 alloy sheet clad on either surface with a low composition aluminum alloy a 1050 or 1070 alloy for example. An extremely thin sheet of pure aluminum laminated onto each side of an aluminum alloy sheet improves the corrosion resistance with little impairment of strength.
They re generally clad with a high purity alloy or a 6xxx series alloy to greatly resist corrosion. As an alternative one side can be clad with a non braze alloy e g. It has a melting point of about 500 degrees celsius or 932 degrees fahrenheit. The thickness of the cladding on each surface may according.
Depending on the desired final properties the core is either homogenized or not before the cladding. The trade name of this aluminum laminate as originated by the aluminum company of america is alcad. An aluminum alloy is a chemical composition where other elements are added to pure aluminum in order to enhance its properties primarily to increase its strength. To the thickness of the core sheet typically represent between 1 and 15 of the total thickness.
Aluminium brazing sheet is manufactured by roll bonding techniques to clad a core alloy ingot on one side or both sides with a low melting alsi alloy. This allows a cheaper metal to be used.